Manuals;
Parabolic Springs Installation
This method is recommended for owners installing their own springs, working on one spring at a time. Those with more facilities may choose to do an axle at a time.
Please read through before starting.
- Loosen slightly the lug nuts of one wheel, but do not remove.
- Jack up your Land Rover’s chassis until the wheel is off the ground.
- Remove the wheel and place an axle stand under the chassis rail, then lower the truck onto the stand.
- Remove the shock absorber from the lower mounting plate.
- Remove the nuts holding the ‘U’ bolts to the axle and/or cut the ‘U’ bolts off.
- Place the jack under the axle to support it.
- Remove the lock nuts and bolts holding the spring eyes to the frame and shackles, then remove the old spring.
- Check condition of the chassis bushing, it should be firmly located in the frame. The shackle plates should have unworn round holes, the bolts should not show significant wear. Clamping plate under the spring should be flat and un-cracked. Check that the new ‘U’ bolts pass freely through the clamping plate holes; we use a full ½” dia. thread that may require slight enlarging of the 7/16” holes on some older trucks. The shock absorber mounting post should be round and parallel to the plate surface. Check shock absorber for resistance if they are to be reused. Check that upper axle buffer is in place and serviceable. NOTE* Warranty is void if axle buffers are not in place. Parabolic’s will lose arc if overextended. Any increase in ride height/shackle length must be accompanied by an equivalent downward adjustment to the axel buffer position. Ensure that the rear check straps are in place and serviceable. Clean and paint reusable parts.
- There can be traces of rubber residue in the spring bushing’s inner 9/16 tube, check the shackle bolt passes through and if not remove residue. The spring eye outer wrap may be tighter at one end than the other, for the front springs install the tightest wrap in the frame mounting horn. This can be important as variations in truck manufacture make some very constricted. If necessary the spring center pin can be loosened and one outer wrap tapped rearward to give a tighter front eye. The upper leaf has a slotted hole for this adjustment.
- Using the reverse procedure bolt the new spring into place on the chassis without fully tightening up. You may need to raise the axle slightly.
- Lower the axle onto the new spring making sure the spring center pin is located into the hole in the axle bracket.
- Install the new ‘U’ bolts and tighten enough to remove slack, do not torque.
- Remount the shock absorber, and wheel.
- At the rear, the check straps should be adjusted so that they stop the downward progress of the axle approximately ½” before the shock bottoms.
- Repeat procedure for other three springs, and with the Land Rover standing freely on its new springs rock the truck back and forth energetically to settle the mountings. Do not expect your truck to sit perfectly level, parabolic springs are more load sensitive than cart type springs which is what gives improved ride and articulation . There may be very slight differences between pairs of springs that you can use to tune your trucks side to side static position. You may wish to position some weight in the truck before doing this to simulate your most common loading of driver, fuel, etc.
- If possible find three adults to stand on the bumper while you tighten the frame and shackle bolts to 70ft./lbs. of torque. Torque shackle lock nuts to the same torque. Torque ‘U’ bolt nuts to 65ft./lbs., repeat for other end of truck. Important ‘U’ bolt torque must be rechecked after first week of use and rechecked periodically afterwards, especially in rough road conditions. Spring’s are not designed to flex across the center section and may fail if ‘U’ bolts become loose. Torque settings are for dry components,anti-corrosion products should not be applied until after tightening, overstressed ‘U’ bolts can lead to failure and damage to axle plate.
- Springs can be lubricated with any used oil to prevent squeaks and coated with Waxoil or a similar product to reduce cosmetic corrosion.
Rocky Mountain front spring pairs are supplied with three 78456UB-S plus one 78456UB-M for the inside right hand axle position, rear springs are supplied with four 78456UB-M.
CAUTION!
Parabolic springs may raise the height of your truck slightly and will alter its suspension performance. Please drive carefully until you are familiar with these new handling characteristics.
As Series Land Rovers are not equipped with anti-sway bars, good quality shock absorbers are necessary to control the improved spring performance. Rocky Mountain has PRO COMP manufacture shock absorbers exclusively for us, to fit our springs. These are based on their 9000 series premium gas shocks, modified to our specification, and offer 2” extended travel.
Service Bulletin; RMPJP010812
SPIN ON OIL FILTER ADAPTER KIT PART# RMP5566
To replace canister type oil filters on LAND ROVER SERIES 11, 11A, 111
This handy oil filter adapter fits Land Rover 2.25 Liter engines equipped with the AC type canister oil filters, and allows for the use of the common spin-on oil filter #ERR3340 as fitted to later Land Rover vehicles.
The adapter body is precision machined from solid aluminum alloy and mounts to the original canister filter head.
The kit includes: CNC Machined adapter body with quad ring, new mounting gasket and new spin-on filter.
Fitting instructions, please read through before starting:
1. Place catch pan under original oil filter, remove retaining bolt and canister and discard old
filter cartridge and oil in an appropriate manner. Retain old canister and bolt.
2. Removed old oil seal from recess in outer rim of filter head and replace with new as supplied.
3. Lightly lubricate new seal and quad ring on inner side of new adapter with clean oil.
4. Thread new adapter's ½ mounting stud into the old canister retaining bolt’s threaded hole.
Ensure mounting stud does not cross-thread in old, and possibly worn, original filter head.
5. Tighten securely using a standard spin-on oil filter removal wrench on the body of the new
adapter
6. Lightly lubricate new spin-on filter seal and install hand tight on new adapter.
7. Start engine and check for leaks, top up oil level.
Ensuring correct fitment and function is the responsibility of the end user.
Warranty is limited to replacement of filter adapter kit only, if found to be defective.
If you are unsure as to the suitability of this part for your truck, do not use it, and return for refund.
Rocky Mountain has made every effort to ensure this adapter will fit all the AC type filter head's as supplied to Land Rover, however we have no control over variations that may have been used over the production run of these vehicles.
Alternate replacement filters available at your local auto parts supplier;
CAN. /US; Penzzoil PZ7, Wix 51068, Hastings LF115, Kralinator L23, Fram PH8A
UK/EU; Purolator L20081, Wix 51068, Hastings LF196, Kralinator L16, Fram PH43
Rocky Mountain replacement window track kit # RM9517K
To replace sliding window tracks on most Series Land Rover applications including;
Rear sliding side windows, doors, truck cab rear sliding window.
Tools required;
Hacksaw or preferably a Miter saw with fine blade.
Small Phillips screwdriver, needle nose vise grips or pliers.
Drill, Pop rivet tool and 3/16” x ¼” aluminum pop rivets.
Angle grinder if required.
New SS screws, 3/16” & #37 drill bits are included with kit.
Eye protection !!!
This installation guide is for Station Wagon rear sliding side windows, for other applications modify instructions as required. A good marine adhesive can be using as a fastening alternative.
Please read through before starting.
- Carefully drill out pop rivets securing upper chrome window latch rails to frame using 3/16 drill bit supplied in kit. Slide rails out of window latches and remove, be careful not to lose latch pins from latches as they are spring loaded and can fall out once they are free of the rail.
- Slide both panes of glass to one end of track exposing as much track as possible.
- Starting with the upper window track, look for the heads of the small slotted screws in the centers of the two window tracks. There will be three or four pairs of diagonally positioned screws securing each side piece to the frame. When the first screws have been removed slide the window panes the other way to expose the screws at the other end of the track. Continue removing the side rail screws the same way.
- At some point you should have enough play to safely remove the windowpanes, if not bend back the old track until you can.
- You may not be able to remove the screws from the bottom track due to corrosion. If this is the case pry up the old track from around the screws and tear it out, this should leave the corroded screws behind in the frame. Use pliers or vise grips to then remove the remaining screws.
- Once all the old track and removable screws are gone, grind down to flush any screws that could not be removed with an angle grinder held length-ways in the old track. Use appropriate safety protection and protect any exposed glass from grinder sparks as they will damage glass.
- To ensure proper draining, use a vacuum or hose to clean out the galvanized drip tray that the bottom track sits on. Ensure that the drain tubes that emerge from the side of the truck are completely clear.
- Cut the new track to fit, preferably in a miter box or with miter saw. The upper track should fit full length; the bottom track will probably need shortening by about ½ inch.The end tracks will have to be cut to length, about 15-1/4”, from one long track. Water trapped in the window track can run out of ends of the track and into the drip tray.
For a more accurate fit of the bottom rail, notch the outer facing side of the ends of the metal channel at the bottom corner approx ½” inwards as per the original track. This can be done with three small cuts, do not cut the rubber track. This is to allow a relief for the fold in the original body skin.
See diagram;
.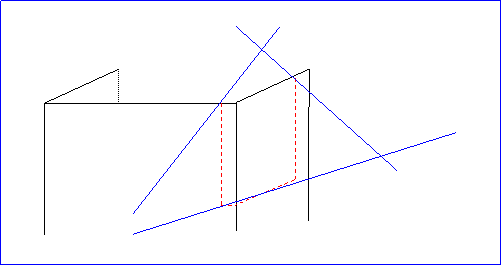
- Position the cut pieces into window frame and drill new diagonal pairs of mounting holes in the centers of the track channels using the #37 drill bit supplied. Use drill carefully to avoid bit breakage. Remove the new track pieces from frame and re-drill the #37 holes in new tracks to 3/16 through both the rubber and the aluminum channel. The holes in the rubber allow the screw heads clearance so they don’t cause a ‘bump’ in the rubber track, the 3/16 holes in the channel allows the screws to sit down close to flush. If desired you can very slightly counter-sink the screw holes.
Alternately you can use pop rivets, or a marine type adhesive.
- Install the bottom track first followed by the side pieces, position the glass panes in the bottom track with the upper track loosely in place on top of the glass panes and push into the frame. Slide the glass to one end and secure the exposed upper track, and reverse to finish the other end.
- Re-install the window latch rails and pop rivet back into place. Track can be lubricated with soap if required.
Thank you for using our product.
RMPREV.0811
|